FMD equipment in use for cable monitoring
Dr. Alexander Weiß has taken over the management of the department Multi Device Integration at Fraunhofer ENAS in January 2021. In the current project “Cable Monitoring”, in which Mr. Weiß is active, equipment is used, which was procured within the framework of the Research Fab Microelectronics Germany FMD.
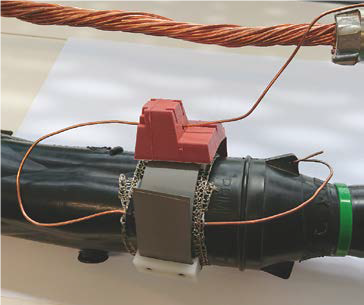
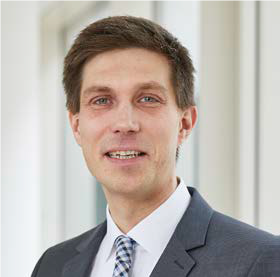
Dr. Weiß, what is your main focus in your new role?
In the first step, I focused on organizational issues and reorganized some processes in the department. Currently, I’m focusing primarily on strategic issues. This also involves our role in FMD. Generally, the department Multi Device Integration (MDI) continues to be a development partner for new types of sensors and actuators as well as their integration into application-oriented systems. With our work in the FMD, we can make significant contributions in the FMD technology platforms “Sensor Systems” and “MEMS Actuators” as well as their broader application. It is also important for us to enhance the state of the art through our expertise in application-oriented research in the fields mentioned before. Furthermore we have to keep addressing future growth fields.
How does FMD support you in your work?
FMD offers our institute and department great added value. This starts with inter-institute cooperation in internal projects and continues with joint initiatives in joint projects and industry cooperation. Moreover, it continues top-down with the wonderful equipment, which was financed by the FMD. I want to mention two examples: our new “test station for MEMS functional testing at wafer level” and our “complex optical analytics cluster for the characterization of optoelectronics systems”.
You work with this equipment in the cable monitoring project. What exactly is being implemented here?
The most fault-prone parts of a wired power system are cable connections and connectors. Gradual degradation of the cable insulation in combination with high voltage increasingly causes partial discharges. These errors usually result in extremely high short circuit currents, and finally destroy the cable connection. The aim of this project is to use novel sensors – in this project, for example, a partial discharge sensor – to develop self-sufficient multi-sensor systems that can reliably detect such faults at an early stage. The sensor nodes consist of a wireless communication module, a current transformer module and various sensors for detecting partial discharges, cable temperature and external influences such as vibrations or shocks. With the test station already mentioned, we are characterizing the MEMS vibration sensors used in the project.
What other project in the FMD universe would you like to be involved in?
We are currently hearing a lot about quantum computing and other advanced technologies. I could imagine us cooperating in the development of quantum optical sensors at FMD.
As a child, I was very fascinated by large machines and what was possible with them. I almost wanted to study mechanical engineering after finishing my school education. But when I visited the Chemnitz University of Technology on Open House Day, I was fascinated by the scientific papers displayed on posters and the small microsystems exhibited. This work was done within the “Collaborative Research Center SFB 379 – Micromechanical Sensor and Actuator Arrays”. I had not seen anything like that before and it was clear to me that this would shape the future. I am even more pleased today that our developments of small sensor systems are also used on large machines, for example for condition monitoring and predictive maintenance.
Last modified: