Robust power electronics for offshore wind farms
Together with partners from industry and research, Fraunhofer IZM is optimizing the service life and maintenance requirements of offshore wind turbines.
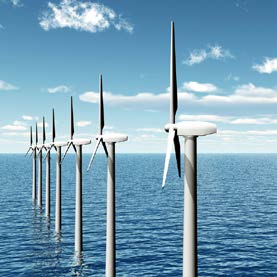
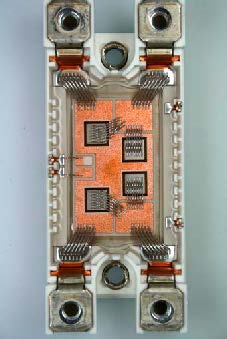
In the context of the green energy revolution, offshore wind turbines play a major role due to their high wind yield. However, harsh environmental conditions such as wind, water, and heat reduce service life and increase maintenance requirements. Maintenance work has thus far been associated with high costs and dangers and can only be carried out in the summer months. Delivery of spare parts is also complicated and expensive. The aim of the AMWind and KorSikA projects is therefore to reduce repair and maintenance costs significantly and extend the service life of the wind turbines.
Condition monitoring with AMWind
The AMWind (Autonomous Monitoring of Wind Turbines) project is developing driver boards for continuous and reliable condition monitoring of power electronic components. The approx. 8 × 8 cm² boards are manufactured individually for each power module, and hardware developed by the Fraunhofer Institute for Reliability and Microintegration IZM evaluates the electrical parameters measured at microsecond intervals, providing information about the exact component temperature. An integrated micro-controller transmits this data directly to the wind farm operator, allowing maintenance work to be planned in good time and efficiently, as well as meaning that measurements can be taken from further distances and in harsh environments, including in the winter months.
Stress tests in KorSikA
In the learning project KorSikA (from the German abbreviation for “corrosion-resistant sintered connection technology for applications at risk of corrosion”), material behavior and the corrosion properties and sensitivity of silver-sintered connections were tested under extreme environmental conditions. The sinter technology had previously been shown in various test processes to be more reliable than the soldered layers previously used. Near-industrially manufactured sintered layers and modules were subjected to the expected temperature fluctuations and humidity loads in the laboratory for a realistic service life of 40 years. The parameters in question were simulated under field-like conditions within a few weeks. The components were then tested for vulnerabilities, thus including the entire value creation chain in the test process.
The analysis produced mission profiles that describe fault mechanisms in detail and that can thus forecast corrosion processes exactly and, in turn, significantly increase the service life of the wind turbines.
Fraunhofer IZM is contributing its expertise in accelerated service life testing, special test methods, material analysis, and condition monitoring to these projects.
About the projects
AMWind is being driven by the following companies and facilities:
• Fraunhofer Institute for Reliability and Microintegration IZM
• Siemens AG
• Infineon Technologies AG
• Technical University of Berlin
• WindMW GmbH
• M&P Gruppe
The project runs from November 2016 to January 2020.
The following partners were involved in KorSikA:
• Fraunhofer Institute for Reliability and Microintegration IZM
• Dr. O.K. Wack Chemie GmbH
• Danfoss Silicon Power GmbH
• Siemens AG
• SEMIKRON Elektronik GmbH & Co KG
• Heraeus Deutschland GmbH & Co. KG
• Forschungs- und Entwicklungszentrum Fachhochschule Kiel GmbH
The project was completed in April 2019 after running for three years.
Both projects were funded by Germany’s Federal Ministry of Education and Research (BMBF).
Last modified: